Leaks in commercial and municipal liners rarely start with dramatic failures. More often, small oversights during design or installation quietly set the stage for costly water loss or erosion. Long-term damage can go unnoticed in containment systems meant to serve agriculture operations, golf courses, or regional infrastructure.
Professional teams can catch problems early by designing smarter, preparing better, and investing in stronger materials from the start. Understanding how large-scale liners fail helps prevent repairs, downtime, and regulatory headaches.
Choose the Right Material From the Start
Material selection always sets the tone for the liner’s lifespan, flexibility under pressure, and ease of deployment. Reinforced geomembranes combine a lightweight structure with high tensile strength, which prevents stretching and failure across wide areas. Many operators also benefit from factory-fused panel systems that reduce seaming requirements and eliminate field welding delays.
A smart material choice supports long-term durability without sacrificing installation speed or affordability. Projects that require wide coverage, such as water district reservoirs or agricultural evaporation ponds, benefit from rolls fabricated into massive, consistent panels. Teams that value efficiency rely on flexible liners that resist UV degradation and perform in varied conditions.
Liner failure often originates where brittle, rigid sheets meet uneven surfaces or shifting loads. Choosing reinforced fabric-backed liners allows for minor movement and contact without tearing or stress concentration. In high-volume applications, it becomes essential to prevent leaks in pond and lake liners before backfill or fill water exposes installation flaws.
Contractors looking for reliability during staging, transport, and deployment value materials that resist abrasions from equipment and handling. Lower seam counts reduce installation time and lower labor costs while improving leak resistance. Materials that balance strength, flexibility, and low weight outperform thicker plastic sheets that struggle on slopes and soft grades.
Prepare the Subgrade With Professional Precision
Before unrolling a single sheet, professionals spend time inspecting and refining the foundation beneath it. Crews use compactors, rollers, and hand tools to eliminate voids, roots, and angular debris that could puncture under load. Every detail of surface prep, from slope tapering to trench edges, supports structural stability once water enters the system.
Field teams often miss the compaction angle when rushing jobs or working around large equipment tracks. Uneven compression across the basin floor leads to differential movement that introduces liner stress during filling. High-stakes containment zones, especially near drinking water or irrigation supply, require laser grading and post-compaction walkthroughs.
Anchor trenches often get overlooked or improperly shaped during prep, creating stress zones where liner edges shift or pull over time. Rolling transitions and trench corners help distribute forces more evenly, particularly in fluctuating fill-level conditions. Professional prep reduces the chance of failures near liner terminations, where movement often begins.
Every smart containment design builds from the ground up, both literally and strategically. Designers who treat the subgrade as part of the system—not just a surface—improve its lifespan and field performance dramatically. Crews who take time to prevent leaks in pond and lake liners through disciplined groundwork reduce repairs, callbacks, and costly delays down the road.
Avoid Common Seaming Mistakes
Even premium liners fail when seams stretch, peel, or separate due to poor bonding. Contractors working in humid or windy environments often struggle to maintain consistent temperatures and pressure for field welding. Wrinkles, dust contamination, or misaligned panels all create long-term risks, even if seams appear sealed at first glance.
Factory-seamed panels offer an ideal alternative when scale and logistics allow. Controlled environments eliminate many variables, allowing for tighter quality standards and broader bonding zones than field welders can typically achieve. In fast-moving jobs, field crews appreciate having fewer seams to test and track.
Problems arise when teams skip vacuum testing, fail to roll seams properly, or overlook overlaps under folds. A single bad seam can introduce years of gradual water loss or lead to total liner separation under stormwater surge. Consistent sealing practices must follow documented procedures across every seam section, no matter how small.
Seams serve as the first place to look when troubleshooting performance issues. Contractors often discover irregularities only after erosion or ponding develops near junction lines.
Carefully reviewing seams helps to prevent leaks in pond and lake liners rather than reacting after the damage becomes visible. Working with a professional liner company like Western Environmental Liner gives you access to prefabricated liners with large-format welded seams for golf courses, irrigation districts, and industrial containment projects.
Account for Environmental Pressures and Water Movement
Liners constantly face pressure, not just from water weight but from wind, slope tension, and hydrostatic fluctuation. Sudden drops in water levels or unexpected overflow events stretch materials unevenly, stressing weak points near inlets and edges. Without reinforcements, even thick liners buckle under variable shoreline loads.
Contractors use slope angles and reinforced edging to fight wind uplift and lateral drift. Ballast tubes, gravel weights, and soil backfill anchor liners where fastening isn’t practical or allowed. For exposed applications, many crews reinforce transitions using batten bars or mechanical strips that absorb environmental force.
Designers also plan for movement where flow concentrates, particularly around culverts, drains, or pump pads. High-velocity flow near slope intakes can gradually strip liner anchoring without visual warning. Extra layering or protective pads guard liners in zones with daily water transfer or mechanical traffic.
Adjusting liner plans to suit the terrain and water behavior always pays off long-term. Wetlands, reservoirs, and flow-through lagoons demand different tension relief zones and edge strategies. Large systems perform more reliably when designers anticipate pressure distribution rather than respond after strain deformation occurs.
Inspect and Maintain Regularly After Installation
Routine inspections catch wear patterns early, especially after major weather or construction activity. Technicians should walk edges, examine slope transitions, and check known seam zones for tension or wrinkling. Documentation matters just as much as detection. Tracking what changed and when helps identify patterns and prevent future damage.
Repair tools vary depending on location, but patch welding and strip overlays work well with reinforced liners. Many jobs also benefit from mechanical clamps or bonding adhesives designed for the liner’s base material. Crews trained in emergency repairs can often handle issues without draining or decommissioning the entire basin.
Digital mapping helps manage complex installations and schedule site visits with minimal disruption. Operators tag inspection zones with timestamps, flags, or GPS-linked checklists for accountability and long-term tracking. Coordinated maintenance protects budgets and reduces unplanned liner replacement across multi-acre sites.
Large-scale liner performance depends on planning, materials, installation, and follow-up. Neglecting any part of that process leads to problems sooner than expected. Teams that monitor liner integrity protect water quality, regulatory compliance, and operational continuity.
Maintenance doesn’t just preserve liners; it extends the value of every decision made during the initial installation. Schedule-based inspections paired with proactive patchwork keep small issues from becoming major failures.
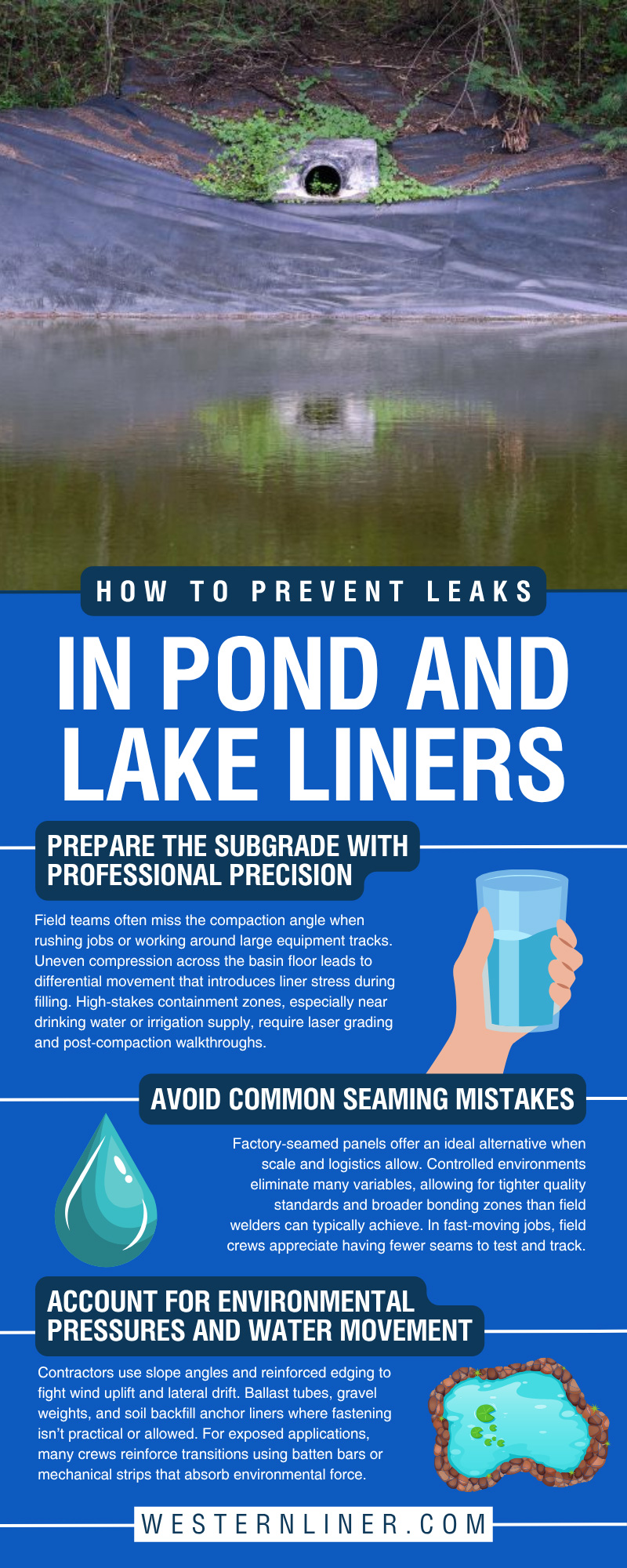